Matthew Conville, M.B.A., P.E.
EASA Technical Support Specialist
Have you ever heard these sayings before:
- “You never get a second chance to make a good first impression.”
- “It is easier to do a job right than to explain why you didn’t.”
- “Quality means doing it right when no one is looking.”
Many of us have heard these sayings and some of us may even use them daily. While they may be used in passing, their true intentions are very significant for a service center. In reflecting on these sayings, we might even begin to ask the question, “How can we embody these sayings in our daily life in the service center?” It’s very straightforward. Completing EASA’s Accreditation Program can check all the boxes for running your business based on these quality mantras.
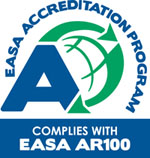
LEARN MORE ABOUT ACCREDITATION
So, what is the elevator speech for the EASA Accreditation Program to a service center’s customer? Very simply, it ensures that the service center consistently performs electromechanical repairs that follow the ANSI/EASA Standard AR100-2020 and EASA/AEMT’s Good Practice Guide to Maintain Motor Efficiency. The result is that customers will receive a repaired electric machine that is reliable and one in which its efficiency has been maintained. Some selling points of the EASA Accreditation program to a service center’s customer include:
- Accreditation affirms the service center’s commitment to excellence.
- Accreditation demonstrates that the service center is dedicated to repairs that maintain efficiency and reliability.
- Accreditation helps validate a service center’s repair work quality, which in turn can give a higher level of credibility to their c ustomer’s supply chain.
When a service center highlights and demonstrates these advantages at customer meetings, shop tours or in industry awareness campaigns, they are positioning themselves to make a good first impression.
One of the first steps in doing a job right is to have an established goal. One of the primary goals of the service center should be to return a repaired electric machine back to its owner with no reduction in machine efficiency or reliability. This is the whole premise of the EASA Accreditation Program. To achieve these goals, we need acceptance criteria to know that work has been done correctly. These acceptance criteria are known as ANSI/ EASA AR100-2020. AR100 is the backbone of the EASA Accreditation Program. This standard is the recommended practice for the repair of rotating electrical apparatus, which is recognized by the American National Standards Institute (ANSI).
After the acceptance criteria has been defined, it’s quite common that there be a guide of some kind to help accomplish the specified criteria. In this instance, the supplemental guide is known as the EASA/AEMT’s Good Practice Guide to Maintain Motor Efficiency. A third party has validated that following these best practices and the ANSI/EASA AR100 standard will ensure that the repair will not reduce the efficiency of a motor that comes in for repair. This has been validated up to and including motors tagged with NEMA’s Premium Efficiency and IEC’s IE3 ratings. When all employees in the shop are using the same documents to define acceptance and how to accomplish those levels of acceptance, the service center stands a much greater chance of getting the job done right. By going through the EASA Accreditation Program, a service center can be at a much lower risk of having those uncomfortable “explaining why we didn’t” conversations with their customers.
Now that a service center stands a greater chance of not having those difficult conversations, how does the service center further minimize the risk? There are several built in requirements to the EASA Accreditation Program that will help a service center achieve the mantra of “Quality means doing it right when nobody is looking.” First, the program requires that a service center train its employees and have documentation showing that the training has been completed. When a service center invests in their employees by training them, they become better equipped to do their jobs correctly the first time. Second, this program requires that internal audits be conducted on an annual basis. When service centers conduct audits, it ensures that they are following EASA’s outlined processes or best practices to achieve EASA’s accreditation goals. When a service center has a third party conduct a mandatory audit every three years to maintain accreditation, it validates from an unbiased source that a service center is performing these processes as prescribed. This validation gives a service center’s customers confidence that the service center is achieving their goals for their repair practices.
If a service center wants to further increase their chances of success for “doing it right when nobody is looking,” the service center will display internal/external audit results, discuss these results regularly with employees and foster an environment of continuous improvement to address process issues as they arise. If a service center embraces what the EASA Accreditation Program is truly about, not only will they be well on their way to accomplishing the three mantras at the beginning of this article, but they will be able to achieve a great deal more. The service center’s customers will have confidence in their repairs, service center management will have confidence in their team’s ability to accomplish their goals and the service center will be well on its way towards long-term sustainability.
AVAILABLE IN SPANISH
ANSI/EASA AR100
More information on this topic can be found in ANSI/EASA AR100
Related Reference and Training Materials
Print