All EASA private webinars are live events in which the audio and video are streamed to your computer over the Internet. Prior to the program, you will receive a web link to join the meeting.
The presentation portion of the webinar will last about 45 minutes, followed by about 15 minutes of questions and answers.
Requirements
- Internet connection
- Computer with audio input (microphone) and audio output (speakers) appropriate for your size group
- TV or projector/screen
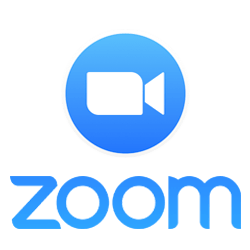
The Zoom webinar service EASA uses will ask to install a small plugin. Your computer must be configured to allow this in order to have full functionality. Please check with your IT department or company's security policy prior to scheduling a private webinar.