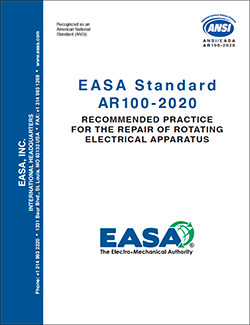
ANSI/EASA Standard AR100-2020
ANSI/EASA AR100-2020: Recommended Practice for the Repair of Rotating Electrical Apparatus is a must-have guide to the repair of rotating electrical machines. It establishes recommended practices in each step of the rotating electrical apparatus rewinding and rebuilding processes.
LEARN MORE & DOWNLOAD